Shuttle BFS System
Shuttle BFS equipment is divided into two types: single-mold and double-mold, with double-mold capacity 1.8 times that of single-mold. According to the form of equipment structure, it is further divided into two types: internal and external cutting, with internal cutting being suitable for the production of PE products, and external cutting being suitable for the production of PE and PP products. The mold takes away the plastic pipe embryo from the extrusion station and transfers it to the filling station to complete the plastic bottle forming, filling and sealing under the protection of Class A air shower, which has the highest market share as the early BFS technology.
- Back and forth movement of the mold between the extrusion station and the filling station.
- Filling areas are protected with Class A air showers, which require monitoring of differential pressure, particles and microorganisms in the shower cabinet.
- Filling areas are protected with Class A air showers, which require monitoring of differential pressure, particles and microorganisms in the shower cabinet.
- Filling by time pressure method, CIP, SIP can be realized.
- The waste rate is generally between 50% and 65% (based on the bottle type).
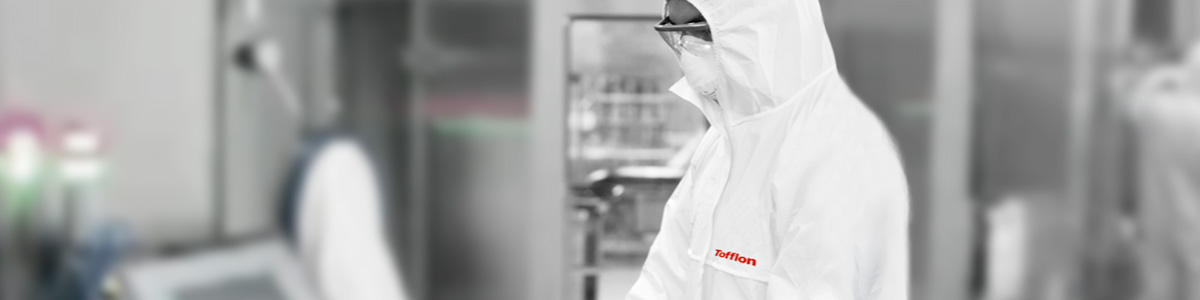
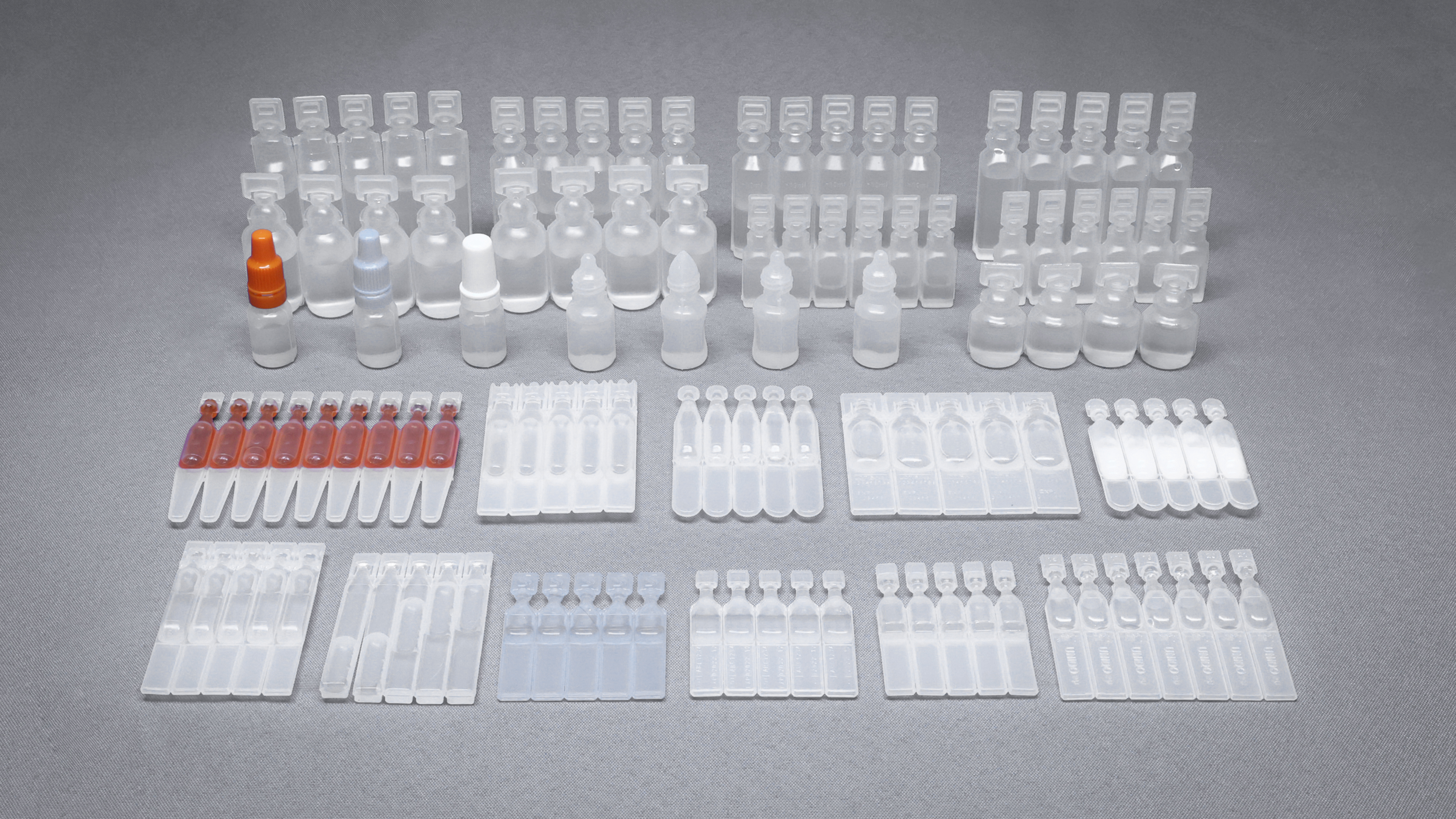
-
1.SVP(PP package).
-
2.Ophthalmic/Otic preparations(PE package).
-
3.Sterile inhalation solutions.
-
4.Cosmetic products.
-
5.LVP.
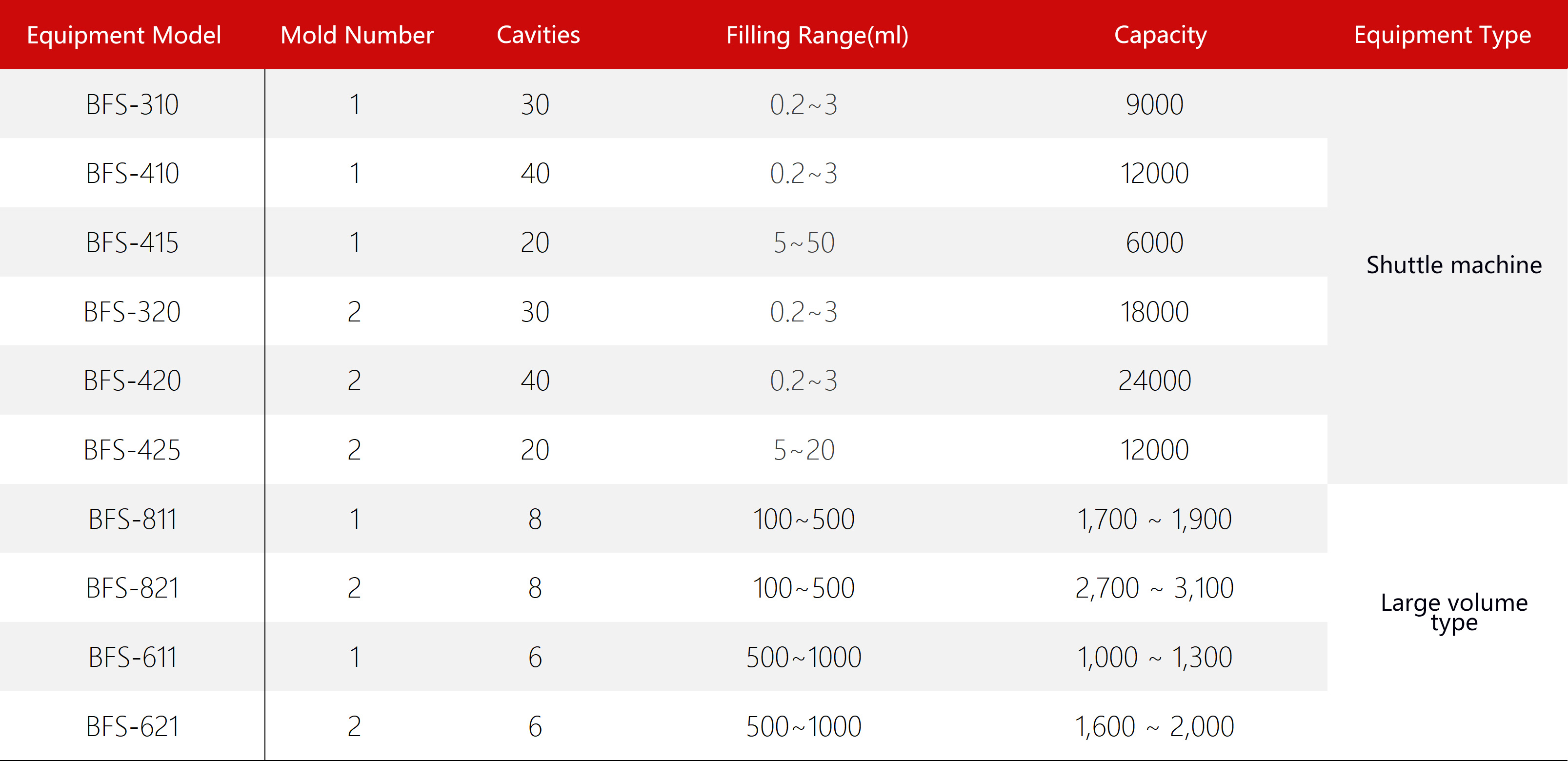