Cage-type Rubber Stopper and Aluminum Cap Washing Machine
As the earliest innovated cleaning device, cage-type rubber stopper and aluminum cap washers are used globally. Tofflon RSS series washers meet the requirements of high-end injection, through the complete new optimization design of the main frame , and the application of the side-mounted motorized door, the external independent support of the cage-type box body, jacketed design, multiple anti-pouring measures technology, having achieved a complete enhancement of the performance, completely eliminating the risk of secondary contamination of the equipment. Meanwhile, in terms of equipment stability, operability, ease of cleaning, verifiability, etc., it brings totally new experience, combined with its wide coverage of output, reliability and security in sterilization and security, which makes the model become the first choice for mass production.
- Mass production, 20 lyophilized rubber stoppers, a wide range of coverage from 10,000 to 240,000 pcs can be achieved.
- Applied in various scenarios such as ORABS、CRABS、ISOLATOR.
- Applied in various transfer of rubber stoppers and aluminum caps.
- Optimized structure design, automatic operation and free maintenance can be realized.
- Side motorized sliding door structure, one-button operation, simple and quick internal cleaning and verification.
- Roller cage adopts independent outside supporting structure, completely eliminating the auxiliary supporting inside the box, avoid the friction caused by the relative movement, and eliminating the exogenous particulate pollution.
- The aspect ratio of the roll cage ≥ 1.2, the dispersed internal material leads to a low stacking height, and the roll cages are easy to clean and there are no extrusion among them.
- Roller cage punching adopts a special process with internal concave surface treatment to ensure smooth inner surface and no damage to materials.
- Adopting jacketed structure design, realizing vacuum replacement drying, water cooling, accelerating the drying and cooling speed.
- Rolling cage suspended rotating process can effectively realize the sterilization process of condensate shedding, minimize the condensate on the sterilization material package, compared with vertical drum structure, it is more conducive to the release of latent heat of the steam, to ensure in the case of complete material sterilization and same amount of material loading, pure steam consumption reduced by 30%.
- Rolling cages rotate slowly, the material is disorderly dispersed, which is more conducive to the drying and cooling of the material, in the case of the same amount of material and moisture content requirements and the conditions of the discharge temperature, drying and cooling time reduce 30% compared with the vertical drum structure.
- Adopting triple anti-pouring technology to systematically eliminate pouring risks.
- Breathing filter realizes on-line sterilization, on-line drying, on-line integrity testing function.
- Equipped with silicone oil automatic quantitative filling system to realize even silicification of the rubber stopper.
- Sterilization control adopts the way of temperature and pressure joint control, the sterilization temperature is more uniform.
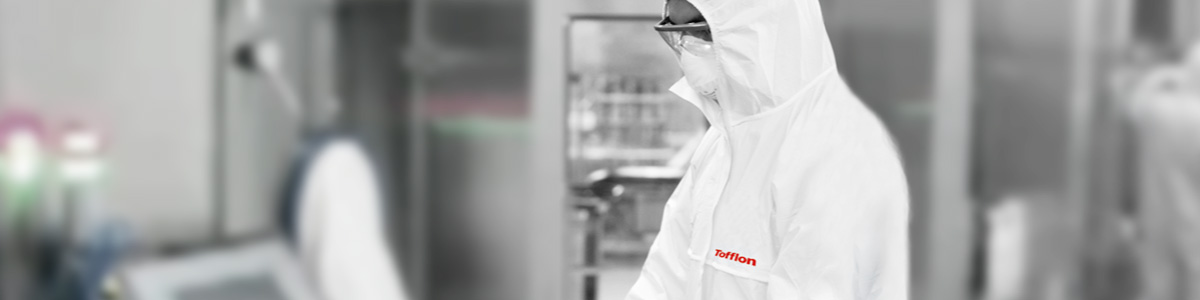